Paint stripping
Paint stripping is a subject that coaters have for many years put to the back of their minds or treated as a time consuming, costly and unproductive exercise. While this may be true to some degree, paint stripping is a vital part of the coating process. Parts must be clean prior to coating. Racks, hooks and jigs must be continuously cleaned to maintain a good earth when used on an electrostatic line and reject parts that have been poorly coated need to be stripped of paint and recoated. To have a good paint stripping system in place will go a long way to improve the overall quality of the finished goods and reduce coating costs.
Paint racks, hooks and jigs need to be designed with continual cleaning in mind. They need to be made from a material that will withstand the constant cleaning that they will endure over their life. The design of the jig is very important, as the idea is to coat the part not the jig. This being the case it is virtually impossible not to have some build up of powder or paint on the jig. This will cause poor conductivity and poor fitment of the parts to the jig.
Depending on the throughput of the jig they will need to be cleaned anywhere from once per day to once per year. Finding the optimum cleaning cycle should be a priority and once found this should be adhered to.
When quoting, Paint applicators and Powdercoaters should allow for a certain reject rate of coated parts (consistent with previous experience) and for the regular cleaning of the associated hooks and jigs. These are real costs and should not be ignored.
Setting up a Paint Stripping Facility within the immediate area of a powdercoat or wet spray line is highly undesirable. Chemicals can be highly corrosive and this can therefore lead to quality problems on parts waiting to be coated or items finished waiting to be despatched. Sand Furnaces and Pyrolysis Furnaces emit ash and dust particles that will also cause poor quality finished parts. If a stripping facility is to be set up in house make sure that it is designed so that there is absolutely no possibility of contamination of the paint line.
The E.P.A. and the local water authority will need to be consulted before a stripping facility is commissioned. It is illegal to wash off chemicals into the storm water or sewer facility and it is likely that the water used to wash parts or jigs that have been through a Sand or Pyrolysis Furnace will contain high levels of metals such as zinc and iron. A waste treatment facility may need to be built to treat the waste water prior to it being discharged. If this is not possible the option of having a contractor come and remove the waste should be explored.
There are four main ways of stripping powdercoat and wet applied coatings. These are –
chemicals
Traditionally there are three main types of chemical paint strippers.
Methylene chloride strippers are used at ambient temperatures and contain additives and either alkaline or acid activators. With the environmental laws being strengthened constantly it is becoming increasingly difficult to treat the waste generated from these strippers. There is also some major health concerns with the use of methylene chloride with some reports listing it as a suspected carcinogen. Methylene chloride is extremely volatile and therefore the tank usually requires a water or wax seal to prevent evaporation. When new these strippers are usually fast acting in removing organic coatings. The removed coatings need to be regularly filtered from the tank to maintain good tank life.
Hot alkaline strippers are traditionally sodium hydroxide (caustic) based and contain surfactants and additives to help in the cleaning process. These strippers are slower acting than methylene chloride and will not strip all coatings. Aluminium and zinc can not be stripped in these strippers. Because the tank needs to be heated the set up cost is significantly more than for that of a methylene chloride tank but the ongoing cost of purchasing the chemicals is significantly less.
Hot PH neutral strippers are also available. These are usually solvent based and can strip coatings from most substrates including aluminium and zinc with little or no etching. These strippers are usually faster acting than the hot alkaline strippers but not as efficient as the methylene chloride strippers. These strippers are usually more expensive than both methylene chloride and caustic based strippers.
abrasive blasting
Various methods of abrasive blasting are used in the paint stripping process. Medias used include dry ice, bi-carbonate of soda, plastic, glass bead, crushed class, sand, garnet and steel grit to name but just a few. The different medias all have different characteristics and uses. A soft media such as dry ice can be used to clean delicate tooling and will produce no damage to the substrate. To clean heavy scale and or paint coatings from a solid steel beam may require the use of garnet or steel grit. The blast pressures are also variable. Blasting a delicate item with high pressures will cause damage. Abrasive blasting is not recommended for the removal of powdercoat from hooks and jigs, as it is usually a very slow process. The pressures need to be high and a hard dense media is required.
sand furnace
Sand furnaces are generally used for the removal of coatings from hooks and jigs. Due to the high temperatures it is difficult to remove coatings from finished goods as damage can occur. Sand furnaces are usually fast at removing the coating. Once the coatings have been removed the hook or jig is usually rinsed in water to remove any residue. This is not always completely successful and there may still be residue left on the items which may cause quality problems once the hook or jig is reintroduced into the painting system. If finished goods are to be stripped in a sand furnace they will need to be thoroughly cleaned after they have been rinsed. This would usually mean having a pickling bath to remove any inorganic compounds that were left on the part and to prepare the substrate for recoating. Sand furnaces are reasonably economical to operate after the initial capital outlay but they have a limited use in a paint stripping operation.
pyrolysis furnace
Jigs and hooks as well as reject parts can be cleaned in a Pyrolysis Furnace. The items are loaded into the furnace and the temperature is set to increase slowly to approximately 420° C. The coatings continue to burn in an oxygen starved atmosphere while the afterburner oxidises the fumes. After a period of approximately two to six hours (depending on the volume of combustibles) the goods are ready to be removed. Ash and any remaining residue are usually rinsed off the parts with high-pressure water. As with a Sand Furnace this rinsing does not remove the entire residue and there may be quality problems when re using the hooks and jigs. Ideally a pickling or abrasive blasting process should follow the burn off process. This will ensure that the hooks and jigs are one hundred percent clean and the rejected parts are suitable for recoating. There is a high capital cost associated with installing a Pyrolysis Furnace and a secondary cleaning process is usually required. Ongoing costs are similar to that of installing a Sand Furnace.
Contact Metalstrip
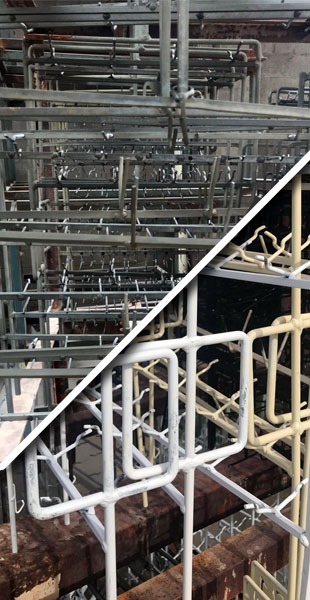
Leave A Comment